Cure in Place Gasket
Applications
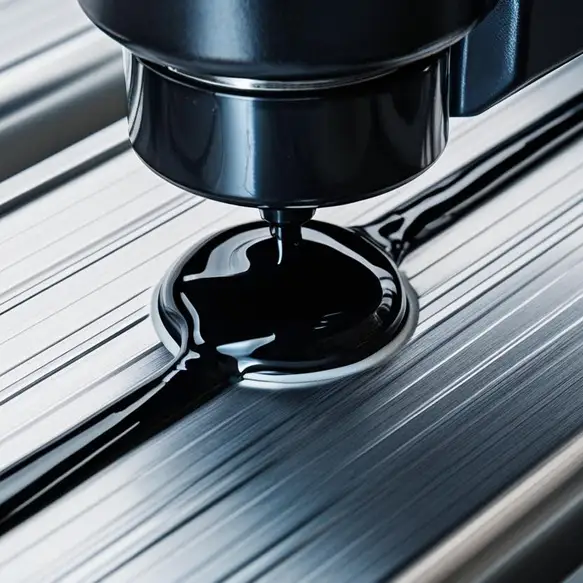
How UV technology is used in CIPG
UV curing technology in CIPG (Cured-in-Place Gasket) applications involves dispensing a liquid UV-curable resin, such as silicone or polyurethane, directly onto a substrate in the desired gasket shape.
Once applied, the resin is exposed to UV light, triggering a rapid photochemical reaction that hardens the material into a durable, flexible gasket. This process ensures precise in-place gasket formation with minimal waste, faster production times, and superior sealing performance.
UV curing also eliminates the need for high-temperature curing, reducing thermal stress on sensitive components and making it ideal for industries like automotive, electronics, and medical devices.
Key advantages of UV curing in CIPG
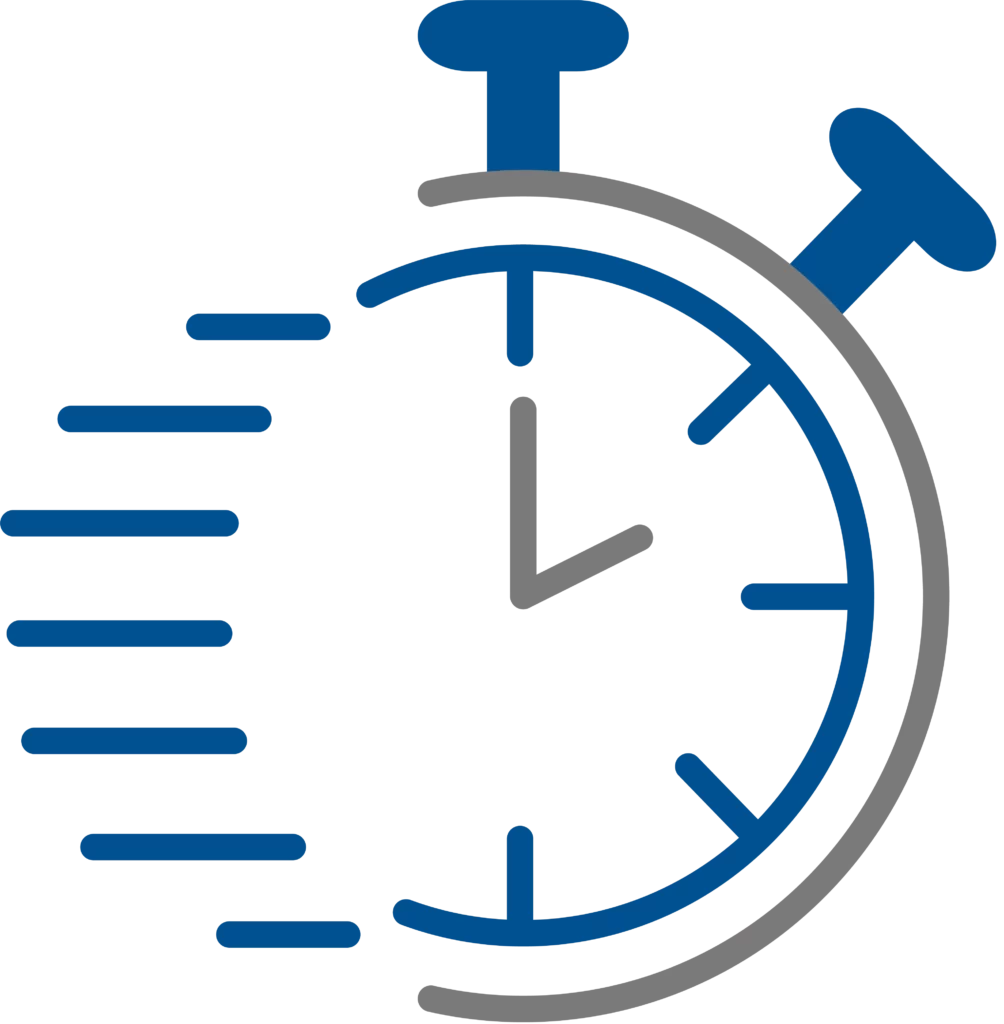
Fast processing:
UV curing significantly reduces curing time compared to traditional heat-curing processes, improving production efficiency.
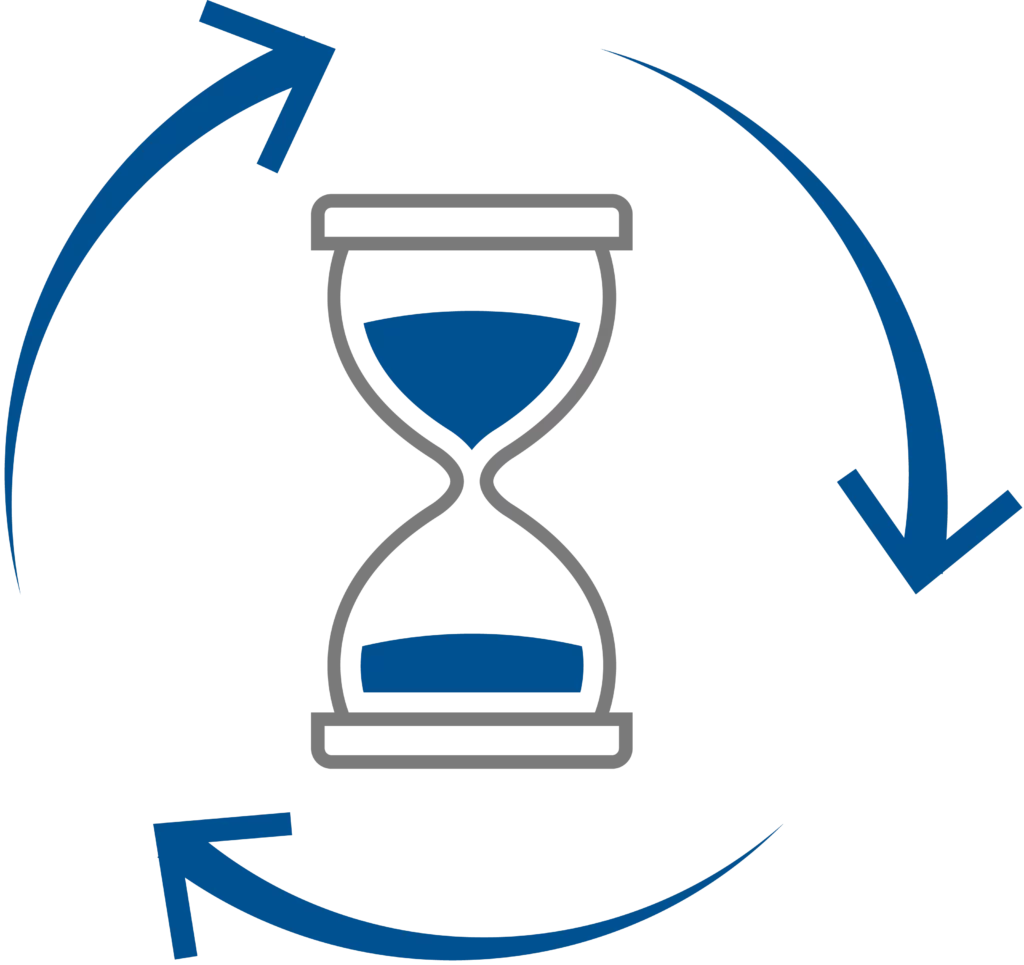
Precision and consistency:
The ability to cure “in-place” ensures accurate gasket shapes and reduces material waste.
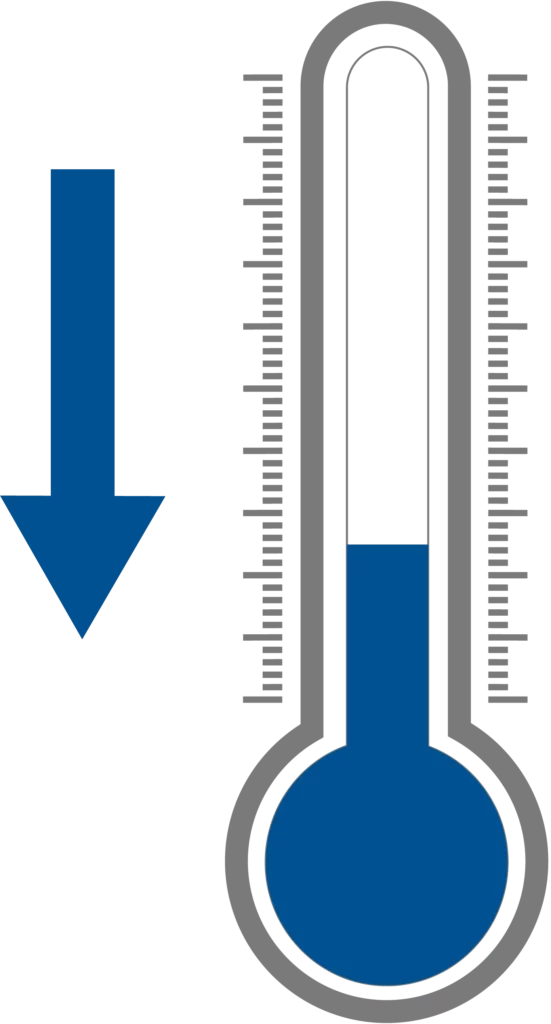
Reduced thermal stress:
As UV curing does not rely on high temperatures, it minimizes thermal stress on sensitive substrates.
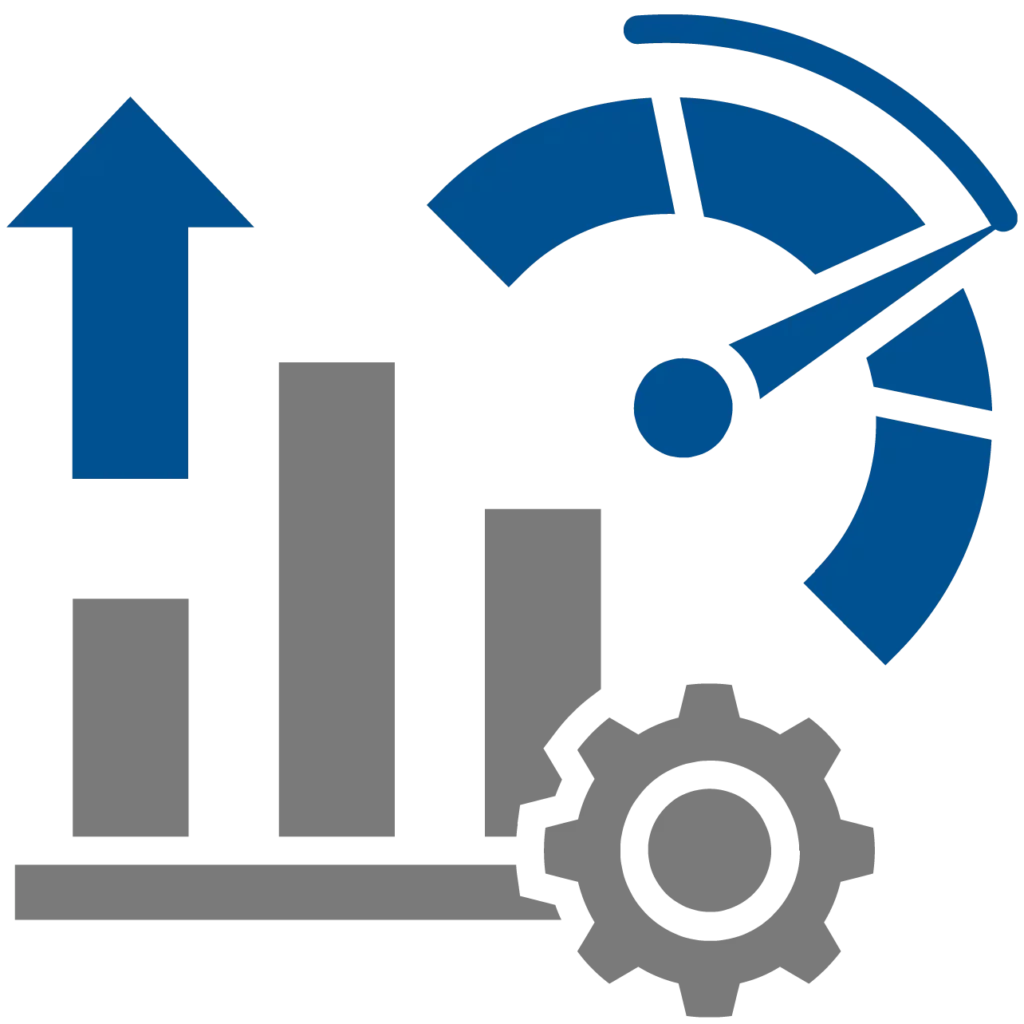
High performance:
UV-cured gaskets exhibit excellent adhesion, elasticity, and durability, making them ideal for sealing and protecting components in automotive, electronics, and industrial applications.
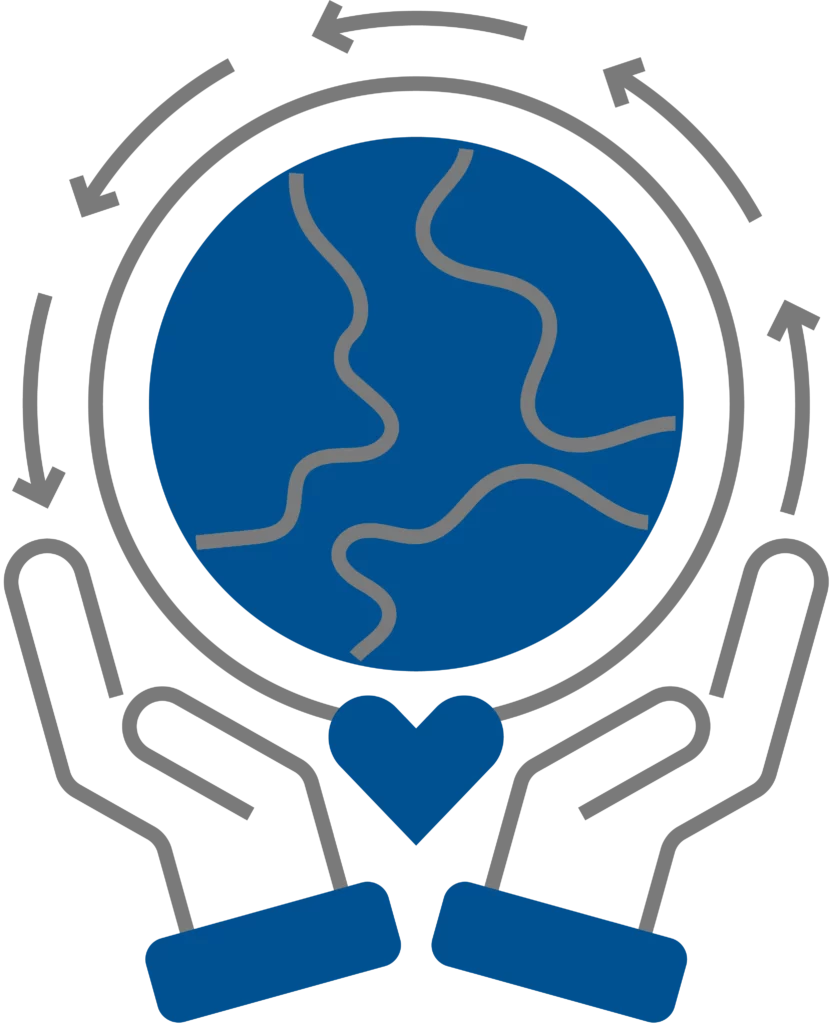
Fast processing:
UV curing significantly reduces curing time compared to traditional heat-curing processes, improving production efficiency.
Our customised solutions
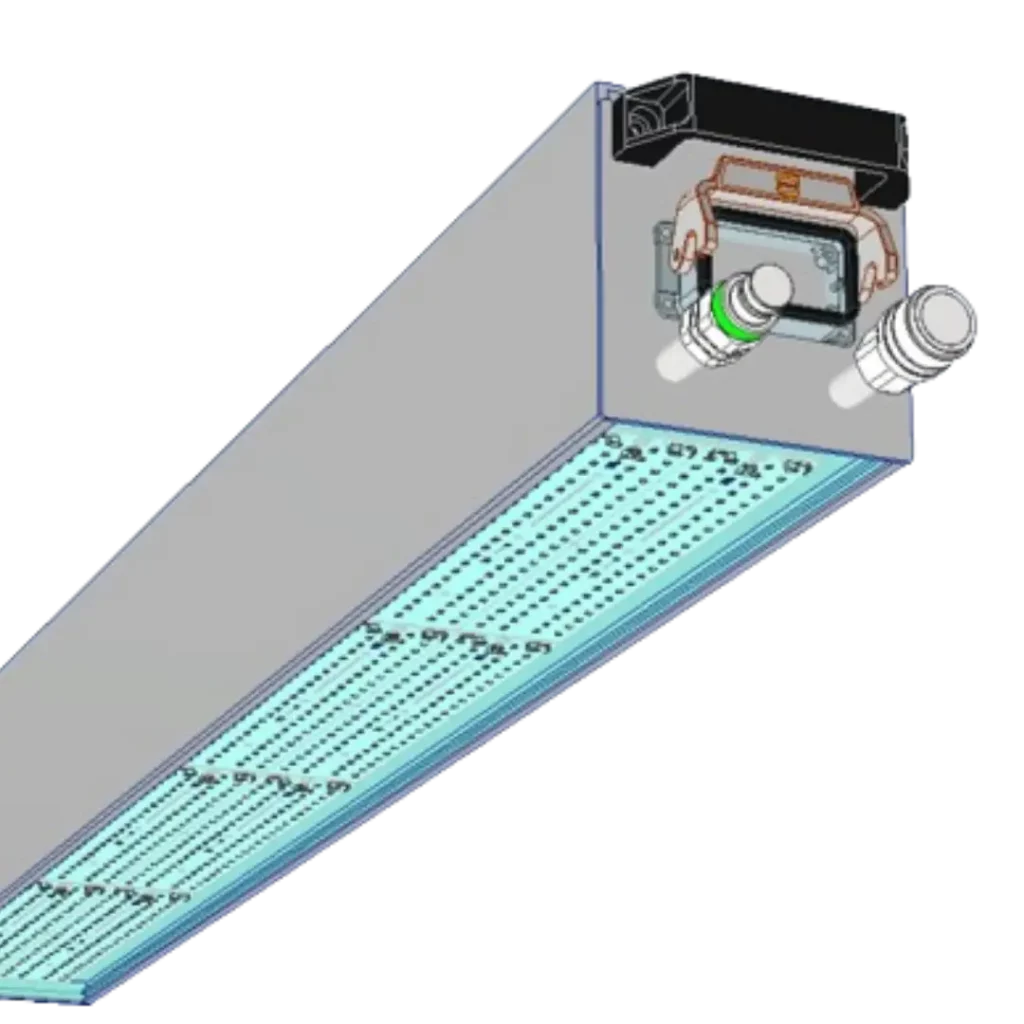
CUSTOM MADE UV LED DRYERS
Air or water cooled UV LED systems with various wavelengths 365 nm, 385 nm, 395 nm, 405 nm. Precise power control from 0.1% to 100%, with Profinet integration
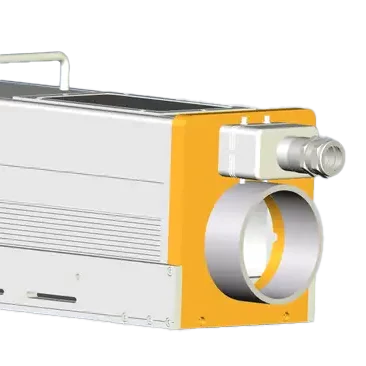
CUSTOM MADE LAMP UV DRYERS
Air cooled high power UV dryers with up to 200 W/cm, advanced electronic ballast
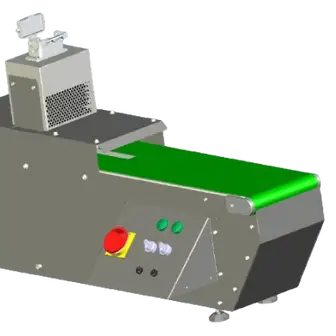
CUSTOM MADE UV TEST BENCHES
UV LED test benches with the ability to simulate real life polymerization cycles, with settings of power, time, distance and wavelength